How and Why to Prioritize High-Margin Repair Work on Your Schedule
Are you struggling to fit all your work onto the schedule? Or giving each work order the same priority, missing out on high-profit work? You may need a better prioritization system, one that prioritizes, among other things, high-margin repair jobs. Prioritizing repair work not only generates revenue but also demonstrates your reliability and efficiency to customers. This article explores the importance of prioritizing high-margin repair work and how to efficiently do it.
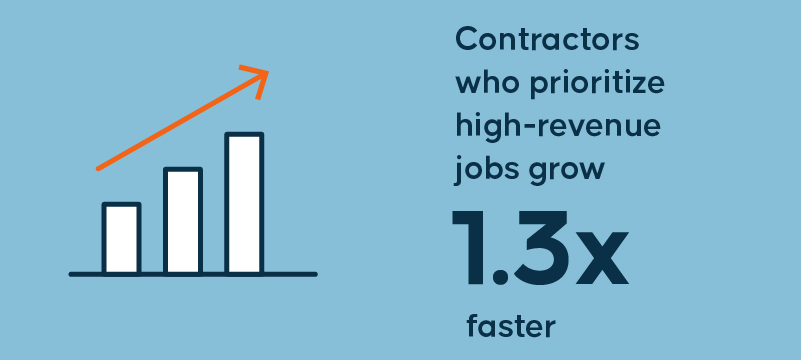
How Prioritizing Repair Work Impacts Revenue
Promptly scheduling and completing repairs is the last step in maximizing revenue from your deficiency management workflow. Repairs are often high-margin work, and data shows that fire and life safety contractors who prioritize this work, earn more revenue per job and grow 1.3 times faster than their lower performing peers.
A contractor who prioritizes repair work ensures that approved quotes are turned into completed jobs quickly. This not only generates immediate revenue but also builds trust with customers, who appreciate the timely response and commitment to their safety. Over time, this reliability can lead to increased customer loyalty and more repeat business.
How Prioritizing Repairs Mitigates Risk
Completing repairs promptly is crucial for ensuring that your client’s facilities meet code requirements and are safe. Delayed repairs can leave facilities vulnerable to hazards, increasing the risk of incidents and potential claims against your business.
By prioritizing repairs, you reduce the likelihood of incidents caused by unresolved deficiencies. This proactive approach not only protects your clients but also minimizes your liability. Additionally, a track record of timely and thorough repairs can serve as evidence of your diligence and commitment to safety in the event of a dispute.
What You’ll Need to Prioritize Repair Work
To prioritize repair work effectively, you need a streamlined scheduling system and clear communication channels. Here’s what to consider:
Efficient Scheduling System: Use software that allows for quick and easy scheduling of repair work. This helps ensure that approved repairs are promptly assigned and completed.
Clear Documentation Sharing: Ensure that technicians performing the repairs have access to detailed deficiency and repair documentation. This enables them to understand the issues fully and perform the repairs correctly.
Customer Communication: Maintain clear and consistent communication with customers about the status of their repairs. This keeps them informed and reassured that their safety concerns are being addressed.
Steps to Prioritize Repair Work
Implement a Scheduling System: Use a scheduling tool that integrates with your deficiency documentation system. This ensures that approved repairs are quickly added to the schedule and assigned to the appropriate technicians.
Set Prioritization Criteria: Develop criteria for prioritizing repairs based on factors such as the severity of the deficiency, customer urgency, and regulatory requirements. This helps ensure that the most critical repairs are addressed first.
Monitor Progress: Regularly monitor the progress of scheduled repairs to ensure they are completed on time. Use tracking tools to keep tabs on the status of each repair and address any delays promptly.
Provide Feedback: After repairs are completed, provide feedback to technicians on their performance. Recognize and reward those who consistently complete repairs on time and to a high standard.
–
Prioritizing repair work is essential for maximizing revenue, ensuring customer satisfaction, and mitigating risk. Want to learn how to get more of this high-margin work on your schedule? Read our guide: The Deficiency Efficiency Guide: 5 Steps to Higher Revenue and Safer Facilities
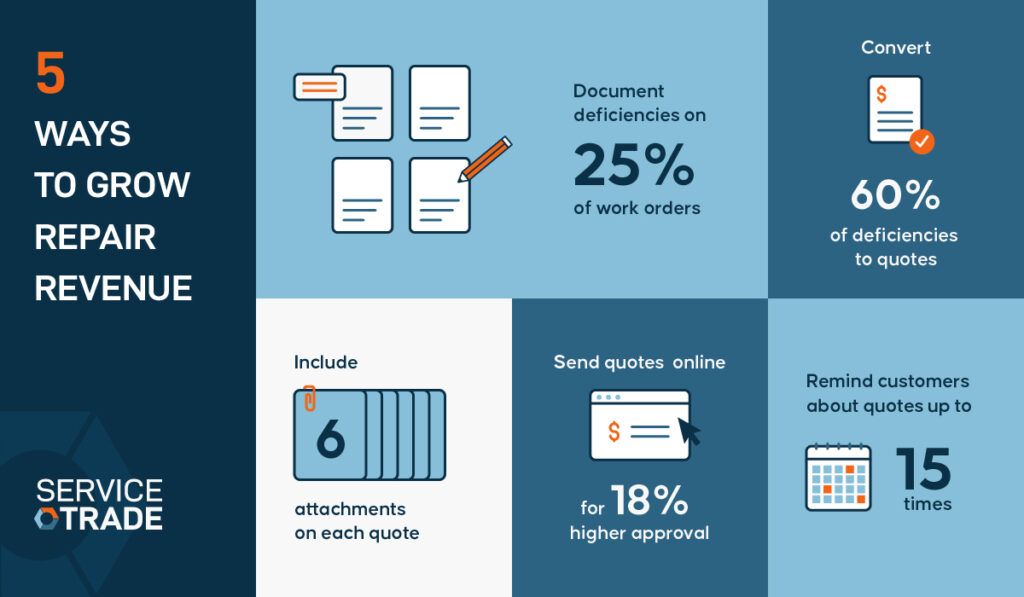
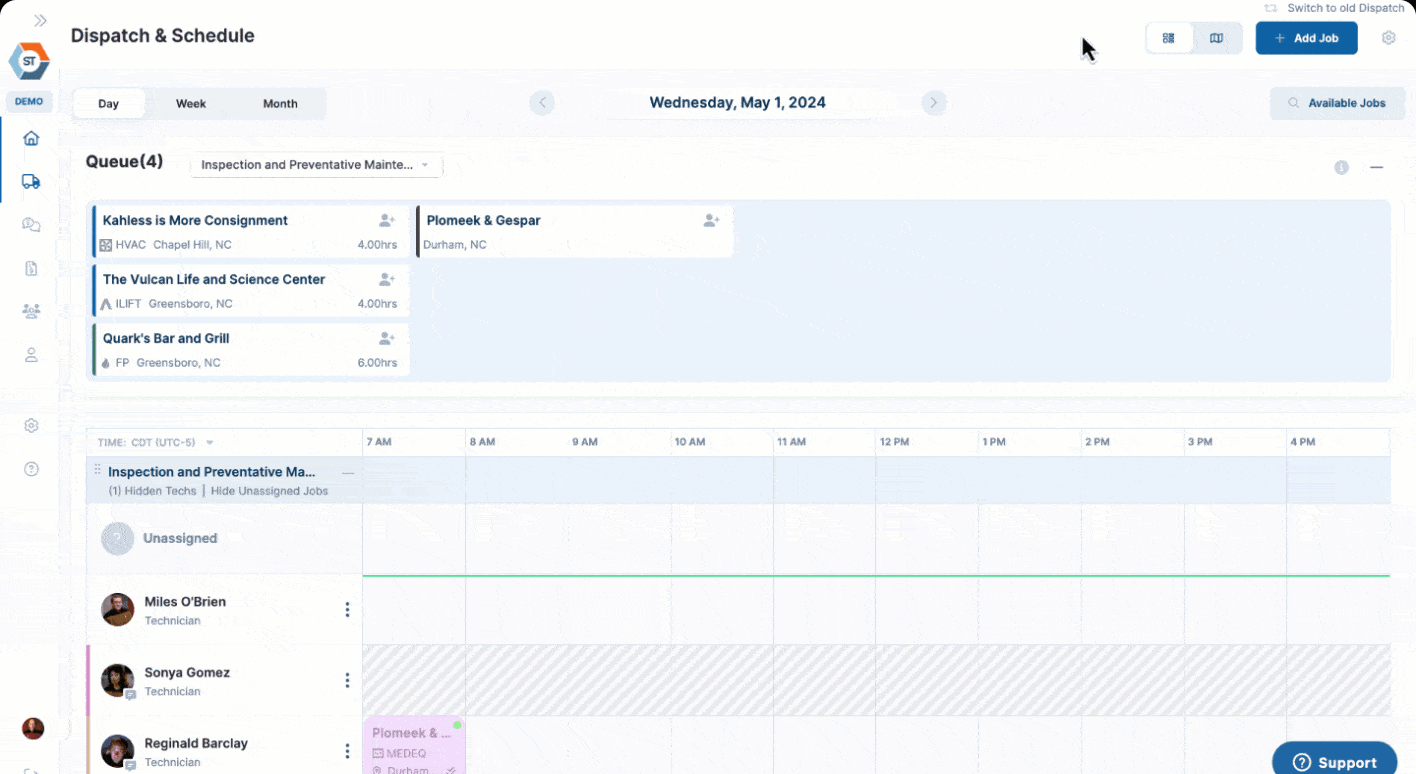
Are your inspection reports still the bare-minimum text? If so, that could be the reason your customers are overlooking deficiencies and rejecting repair proposals. Your customers are becoming increasingly accustomed to images and videos. That means the way you capture and present data in both inspection reports and quotes can make a significant difference. Enriching […]
Fire and Life Safety Contractor A sends 30 repair quotes a month with a 60% approval rate. Contractor B sends 5 quotes with a 100% approval rate. Which contractor is scheduling more high-margin repair jobs? Contractor A, of course. That’s because, while important, quote approval rate can be a deceiving metric. According to our data, […]